By Leslie Lee
What does a $350 water filter capable of removing microscopic contaminants from 1,300 gallons of water a day look like? To the untrained eye, it looks like a large sheet of paper rolled-up inside a pipe, similar to a classroom craft supply perhaps.
These paper-thin filters, called membrane filters, are actually made of multiple layers of permeable polymers. An average filter module contains about 85 square feet of filter surface. Placed in pipes that water is pushed through at high pressures, these filters are hugely important to Texas water.
As water suppliers have built water reuse and inland desalination plants throughout Texas, new treatment infrastructure was needed to continue providing enough high quality water. These plants cannot function without such rigorously tested water filters; many water plants use about 100 of them simultaneously throughout their facilities and daily processes.
According to state water planners, to keep Texas water secure, desalination and reuse will be two of the major technology-dependent tools bridging the gap between future water demands and strained supplies.
“There is a lot of brackish groundwater in Texas,” said Dr. Shankar Chellam, who is the J. Walter “Deak” Porter ’22 and James W. “Bud” Porter ’51 Professor in the Zachry Department of Civil Engineering at Texas A&M University.
“And during the 2011 drought, even a lot of surface waters became more brackish; no rain, lots of sunshine and high evaporation results in increased salinity in surface waters. So, how do you remove the salt content from these waters?”
Reverse osmosis (RO) and nanofiltration are how, and there are currently 47 major inland brackish desalination plants in the state using those technologies to supply high quality water to residents, according to the Texas Water Development Board. Chellam and his team study the filters and processes involved in RO and nanofiltration.
Their research shows that precise, plant-specific protocols using advanced technologies and a series of filters can perfect these filtration processes, protecting consumers from filtration failures and possible resulting water contamination, while also benefiting plants with more cost-effective systems.
“We are examining how to tailor the process to the particular kind of water you need to desalinate at a particular plant,” Chellam said.
Basics of modern large-scale water filtration
Chellam’s team studies the various water purification uses of polymer membrane filters and their related applications, including desalination, water reuse, disinfection, and removing turbidity, microorganisms and chemicals.
“Polymer filters are the cheaper variety of advanced water filters, and they are the most implemented, so we exclusively work with those,” he said.
Because research on the fundamental scientific principles of advanced water filtration is still greatly needed, Chellam said, the National Science Foundation (NSF) and the U.S. Department of the Interior have funded multiple projects conducted by his team.
The most common advanced water filtration processes used today are RO, nanofiltration and microfiltration/ultrafiltration, Chellam said.
- RO is used by many seawater desalination plants and is “very expensive and energy-intensive.” It involves pushing saline water under high pressure across a dense membrane, i.e. one with no pores. The clean water preferentially flows through the filter, and the salt does not, thereby achieving desalination.
- Nanofiltration involves pushing brackish or surface water across a membrane with tiny pores to remove contaminants as small as 0.002 microns (2 nanometers), he said. This is typically used for removing hardness and organic compounds. It is similar to RO but less expensive because it operates at much lower pressures than RO.
- Microfiltration involves filters with pore sizes larger than about 0.1 microns. It is similar to ultrafiltration, which spans the range between microfiltration and nanofiltration. These processes require much less energy and are relatively widely implemented in Texas for small- to medium-sized drinking water plants. “It is less intensive than RO but sufficient for many plants,” Chellam said.
One important factor for water providers’ considering these options is that filters with smaller pores require more pressure to push the water through, and therefore bigger pumps and higher energy costs.
“The idea is to use the least pressure possible, so that your energy costs are low,” he said.
Perfecting the ideal process
Chellam has found that generally the most efficient way to begin the water filtration process is with coagulation, which clumps together small contaminants, making them bigger.
“We’ve been looking at a technology called electro-coagulation,” he said, most recently in a study funded by the Interior Department, studying the practice for use in inland desalination plants.
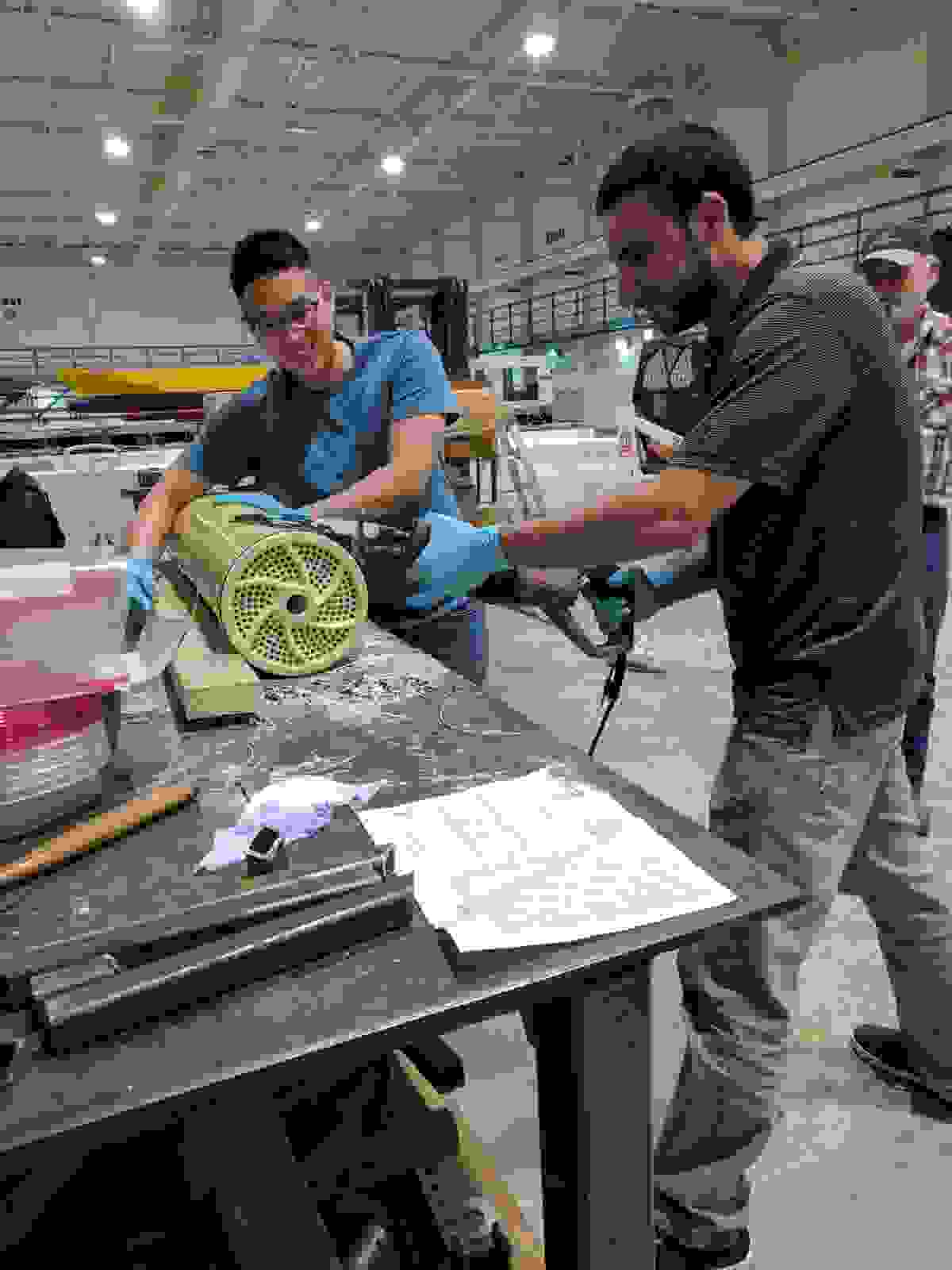
Electro-coagulation uses trace amounts of aluminum (or other configurations) to bind many small contaminants together into larger clumps. This water is then treated through a series of filters, beginning with a course filter, meaning it has large pores. This filter is able to catch the contaminants because they have been coagulated together.
Then the process continues with pumps pushing the water through finer filters. The coagulation and pretreatment processes save energy resources and costs by minimizing fine-filter use and high-pressure pumping needs, Chellam said.
The final step is to filter the water through an extremely fine filter. RO is needed for this final step at seawater desalination plants, he said, but the cellular make-up of inland brackish groundwater allows for nanofiltration, to be used.
“Most of the salt content in seawater is from sodium and chloride, and for that you need to use RO,” Chellam said. “But in many inland sources, the salinity comes from sulfate and calcium, which don’t need RO. So, you can reduce the salinity just by doing nanofiltration, which is more energy-efficient.”
Chellam describes this entire progression as an “integrated, hybrid process,” and his team has found it to be ideal for inland brackish water filtration.
“I believe more and more people will use this or similar processes as pressures on water supplies increase and as water quality worsens.”
Clogs happen
Researching and perfecting these filtration protocols makes plants more efficient, but Chellam said dealing with clogs and filter failures is also part of his research.
“These filters will clog rapidly if everything is not completely in-sync,” he said.
Planning clog prevention and remediation into plants’ automated system protocols is part of Chellam’s work. Reversing the water flow direction in pipes can de-clog a filter, but that can result in slowing down the process. Analyzing and perfecting this process requires “reducing the clogging rate versus increasing the volume of water filtered,” he said.
I believe more and more people will use this or similar processes as pressures on water supplies increase and as water quality worsens.
“The idea of filtration is to remove stuff,” he said. “And the more stuff you remove, the faster a filter clogs. So how do you de-clog and regenerate the filter? How do you maximize the water productivity of a filter? We are researching that.”
Chellam’s team conducts “autopsies” on failed filters that plant operators send in for examination.
“We cut these filters open and find out why they clogged,” he said. “You can use spectroscopic methods and microscopic methods; you can do some advanced surface chemistry and surface physics to compare the brand new filter and the clogged filter. And then you can understand what you can do and how you should adjust your process to remove all these items that clogged your filter.
“Once we identify what’s clogging it, now the question is, why did the pretreatment process not remove it? Where was your pretreatment not good enough? How can you tweak it or replace a part of it? How can you clean the materials that clog the filter? Maybe you did not have enough safeguards against this particular contaminant that is fouling your filter and you need to implement something else.”
The future of filtration
Another question that Chellam has been researching is: how can viruses, the very smallest kind of microbial pathogen, be more effectively removed from water supplies using a filter and low pressures?
Currently, drinking water plants use chlorine or other disinfectants to inactivate viral pathogens. However, chemical disinfectants produce potentially carcinogenic byproducts via side reactions, he said. Using membrane filters to physically remove microorganisms would reduce the need for chemical disinfectants and decrease undesirable toxic byproducts in drinking water.
His team is working on three filtration-related projects, two funded by NSF and one by the Interior Department. One is studying how virus shapes, sizes and surface characteristics/charges affect filtration efficacy. Virus filtration is a relatively new field, and the NSF and Chellam are still seeking full, fundamental understandings of how viruses behave in filtration systems, he said. In another project, Chellam’s team is looking at optimal filter regeneration by flow reversal, or backwashing, to remove previously filtered materials that clog the filter. The third grant is for performing autopsies on actual filters from real-world membrane facilities to better understand the clogging process and to propose innovative cleaning models, Chellam said.
He believes that the need for advanced water treatment technologies will only grow in Texas.
“What used to be freshwater isn’t as fresh anymore, and many cities are looking to alternative sources, so we will need higher and higher technology levels to purify these strained water supplies.”